Sparrow RC Car
Shock Tolerant, Self-Stabilizing
Principles of Engineering Course Project
A robust, RC car built as a five member, interdisciplinary team over half a semester. Sparrow was designed to be driven off high places and stabilize through gyroscopic wheel action. As the chassis design and fabrication lead, I was responsible for the design of a shock tolerant final vehicle frame in the Solidworks CAD program and its fabrication in the Olin machine shop.
Chassis rendering from an early sprint. In this iteration, the main deck was still to be made from MDF or plywood. In addition to this, the springs being used were in a U shape around the bottom of the axles. This proved to be ineffective once I received the spring steel I would be using and learned the steel would not easily buckle.
Final rendering of the Sparrow chassis. In the final version, the main deck transitioned to a sheet metal plate that could easily be manufactured with a CNC plasma cutter. The leaf-springs transitioned into O's to utilize the spring steel's bending action rather than buckling as before.
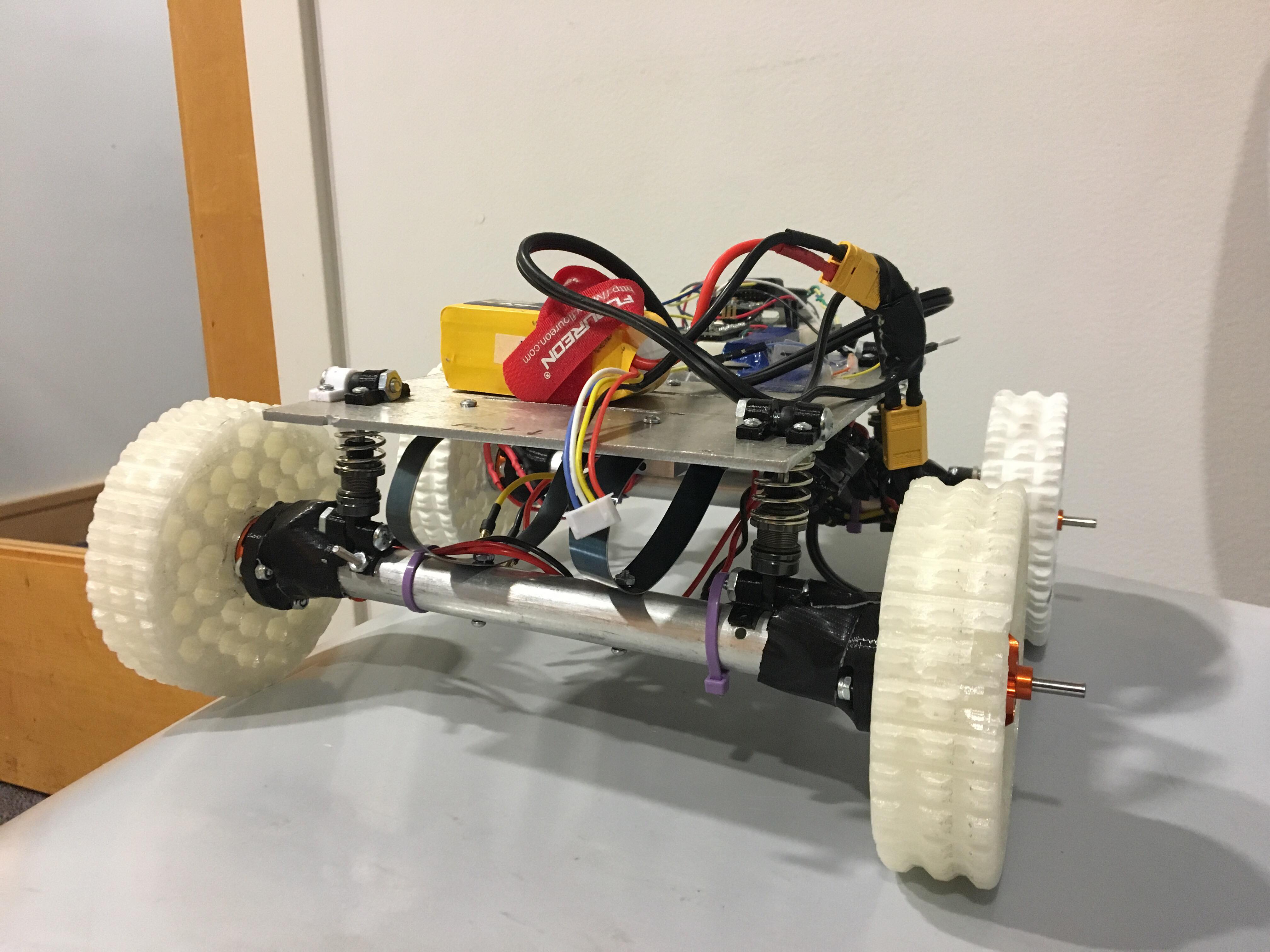
Completed vehicle with electrical hardware mounted. An Arduino Nano and an IMU were used to find the angle to be corrected during free-fall. The system was powered with a LiPo battery and an additional moter in the center controlled the roll while the spinning of the wheels controlled pitch.
An example of the Sparrow in action. The vehicle applies torque in the clockwise direction to cancel out and correct the initial counter-clockwise spin.
The Sparrow was an opportunity for me to exercise the lessons I had learned in mechanical design and manufacturing in my first year of Olin. Determined to build this thing the "right way" the first time, I spent a great deal of time outside the machine shop ensuring that the design was perfect before fabrication began. Through this method I spent a lot less effort on large reworks later in the project and instead could focus on fine tuning the smaller parts that allowed the system to eventually perform effectively.
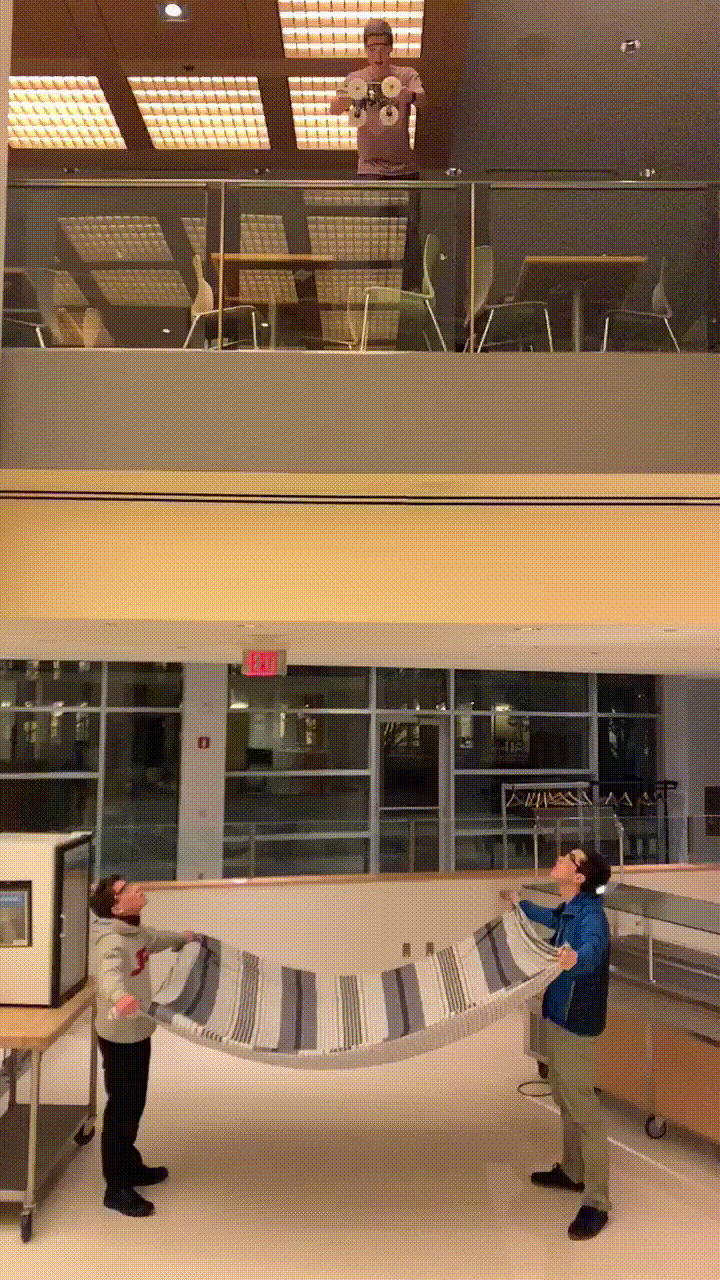